by Brianna Crandall — May 26, 2014—A lack of communication—combined with a short-sighted fixation on holding down factory capital expenditures—is incurring massive energy-inefficiency costs for manufacturers during the lifetimes of their production facilities, according to global information company IHS Technology
“There is a significant disconnect between those who make decisions regarding industrial capital expenditures, and those who are tasked with managing the costs of manufacturing operations,” said Alex Chausovsky, manager and principal analyst, Motor-Driven Systems and Industrial Automation, at IHS. “Individuals making capital-expenditure decisions when building new industrial facilities rarely, if ever, consider the long-term costs associated with projects.
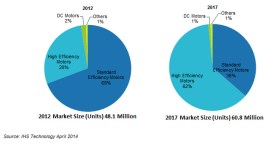
High-efficiency motors accounted for only 28% of global low-voltage motor shipments in 2012, but by 2017, the higher-efficiency motor types are expected to grow to represent 62% of shipments.
(Click on image to enlarge)
“As a result, these decision makers consistently place initial purchase price concerns ahead of total cost-of-ownership (TCO) considerations. This means that energy efficiency is not a factor in the decision-making process, and operators that take over these projects after their completion are often faced with much larger energy bills than they would have if the most efficient equipment had been specified during the construction phase of the project.”
For factory operators, these energy bills can add up over the years, says IHS. For example, the purchase price of an average electric motor used in a factory represents only 2% of the motor’s lifetime costs. However, a full 96% of the motor’s TCO is accounted for by its lifetime electricity usage—with the remaining 2% going toward repair and maintenance, according to multiple industry case studies.
Electric motors used in industrial facilities and other settings consume nearly half of the world’s electricity, according to the International Energy Agency (IEA). Furthermore, industry represents the largest single electricity-consuming market, with 42% of total usage in 2006, vastly exceeding other areas, including residential and commercial.
Motor rundown
The electric motor segment represents a vast and growing portion of the industrial market. Global revenue for low-voltage motors used in industrial applications is set to rise to $23.4 billion by 2017, up from about $14.6 billion in 2012. However, the product mix is expected to change greatly during this period in terms of efficiency class, due to various Minimum Efficiency Performance Standards (MEPS) being enacted by governments around the world.
As presented in IHS’s 2013 Low Voltage Motors report, in 2012, high-efficiency motors accounted for only 28% of global low-voltage motor shipments. Most of the remainder was standard efficiency motors. By 2017, the higher-efficiency motor types will grow to represent 62% of shipments, says HIS, as shown in the graphs on this page. Industrial motors are used in a wide variety of applications, including fans, pumps, compressors, mixers, blowers, extruders and injection molding, notes IHS.
Efficiency deficiency
Motors serve as just one high-profile example of the problems caused by the disconnect between industrial capital expenditure and operating expenditure teams, says IHS.
“In general, improvements in industrial energy efficiency (IEE) can increase productivity, allowing companies and countries to compete more effectively in the global marketplace,” Chausovsky said. “IEE represents the low-hanging fruit in total energy efficiency gains, with minimal implementation barriers that can be overcome while remaining fiscally responsible. Capital investment in IEE can often be recouped in short periods of time, often less than 24 months.”
Bridging the communications gap
To help lower operating expenses, companies must consider the total cost of ownership when purchasing new equipment, concludes IHS. By purchasing slightly more expensive gear that is more efficient, manufacturers can save massively on electricity costs over the years.
Equipment suppliers, for their part, can encourage the adoption of high-efficiency equipment by offering flexible payment options that allow buyers to pay off the gear over time as they attain TCO energy savings.
For example, Siemens Financial Services in a partnership with the Carbon Trust offers a program in the U.K. that is designed to minimize financial risk to the customer, says IHS. Through the program, customers can purchase or lease energy-efficient equipment at a price that results in a net-neutral or net-positive cash flow for the buyer.