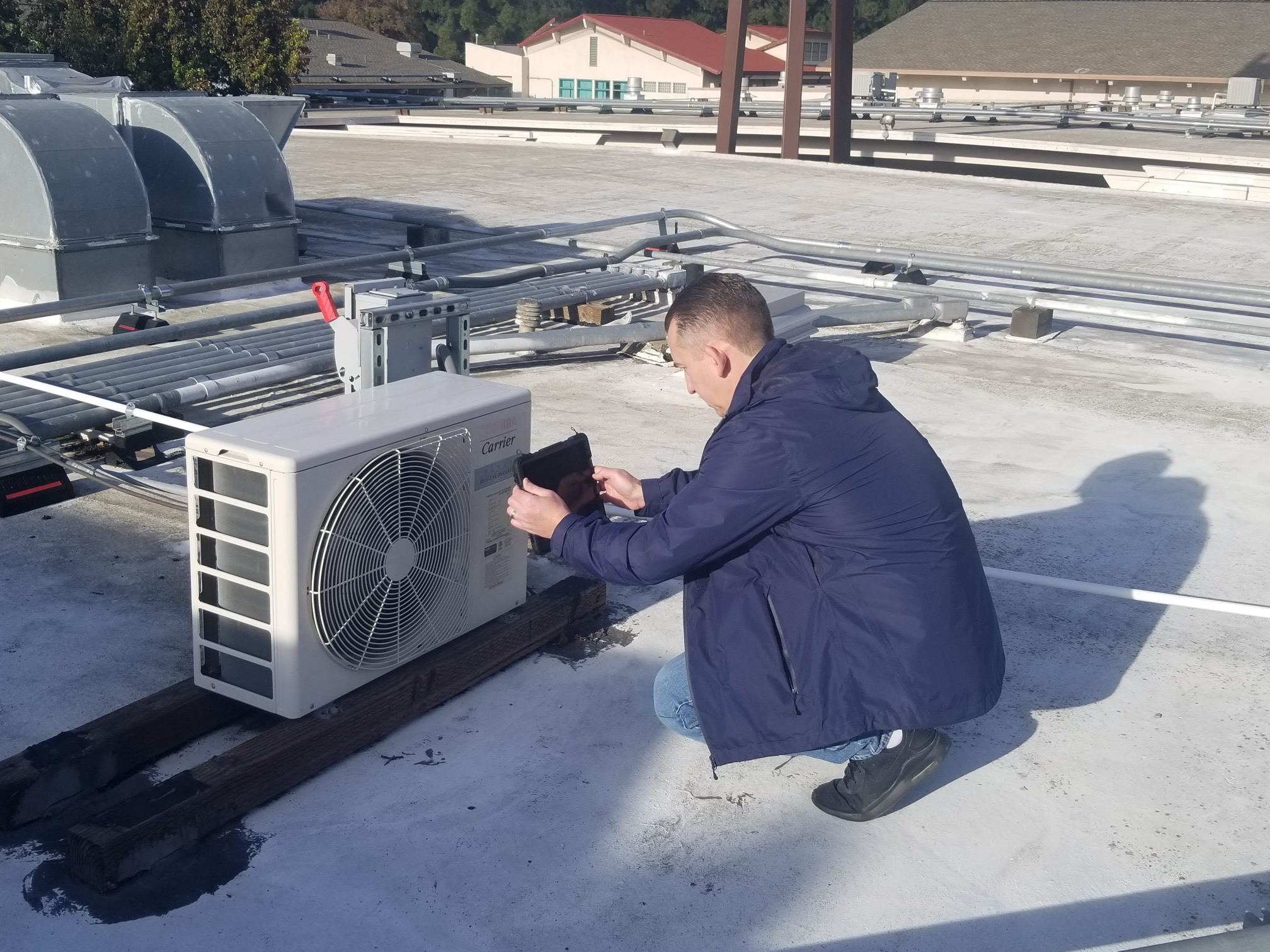
By Jonathan Styrlund, ARC Facilities — As artificial intelligence (AI) becomes an increasingly popular topic, facility management (FM) professionals are asking themselves: How does AI fit into their daily work? Should it? How or why should they use it?
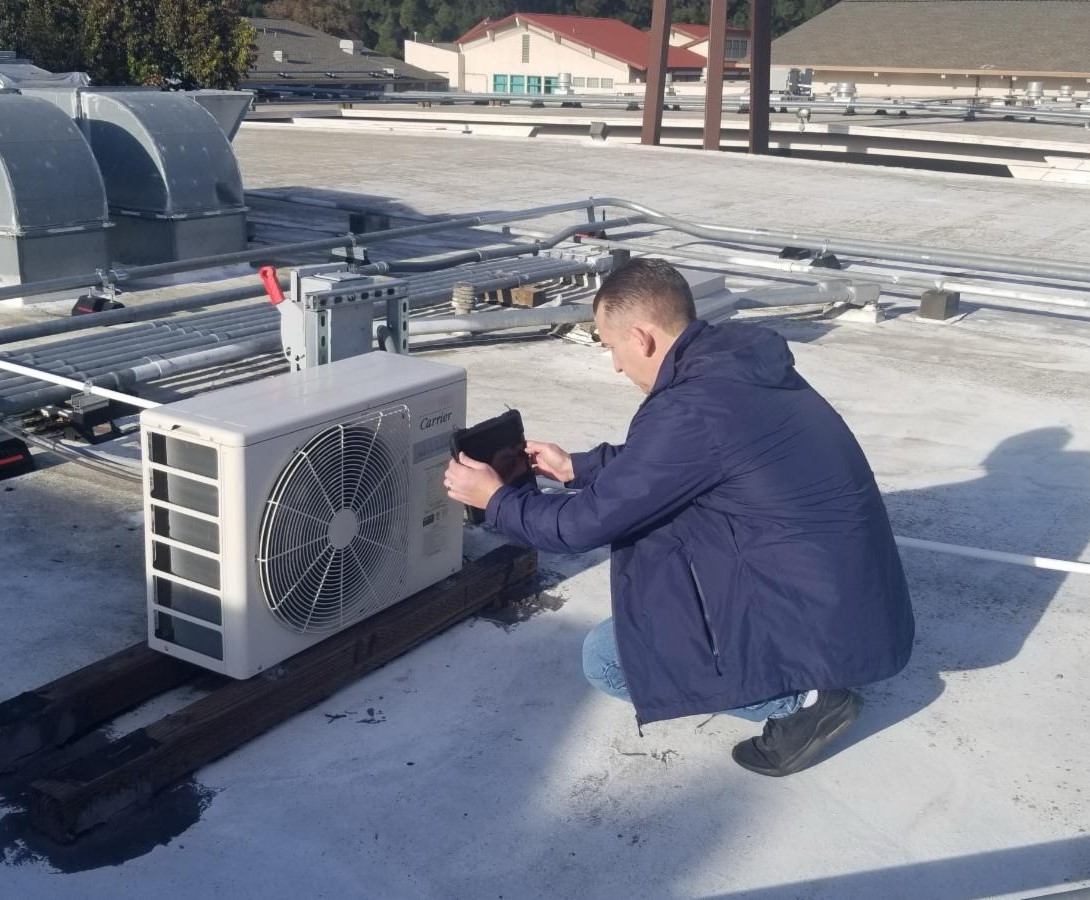
Imagine walking up to a piece of equipment and instantly having troubleshooting tips, parts schematics, or installation and warranty information. This capability is a major value-add AI can bring to FM. Image: ARC Facilities
Large organizations might view AI as an expansive solution aimed at integrating all operational tools or analyzing massive data sets. This approach doesn’t necessarily serve the needs of frontline technicians. Unlike high-level integrations intended for C-suite efficiency and analytics, facility management must prioritize actionable, immediate solutions that directly affect the people on the ground — the technicians.
For many in FM, particularly technicians, there is a notable hesitation around AI, not out of fear, but because most AI applications aren’t relevant to their day-to-day tasks. Technicians spend their time fixing equipment, diagnosing issues, and maintaining systems. Their days aren’t filled with data analysis or report generation, so they don’t require tools that promise enterprise-level insights. Instead, to be beneficial, AI for technicians needs to focus on practical, intuitive applications that can improve workflow efficiency and reduce downtime without requiring significant training or time investment.
Understanding technicians’ relationship with AI
Most technicians in FM are not technology enthusiasts. They’re not likely to spend their weekends exploring ChatGPT, Dall-e, or Gemini, or diving into tech blogs for fun — they’re busy solving hands-on problems. For many techs, their approach to AI is simple: if it can help do their job faster, it’s worth considering. In this respect, AI adoption in FM doesn’t need to focus on replacing tasks but rather, on assisting them.
Ryan Koppelman, VP of Technology, eCIFM Solutions, Inc. explained at IFMA World Workplace:
Generative AI can revolutionize how designs, layouts, and workflows are developed and optimized. Facility managers and designers can leverage generative AI to explore multiple design possibilities and select the most efficient and cost-effective solutions.
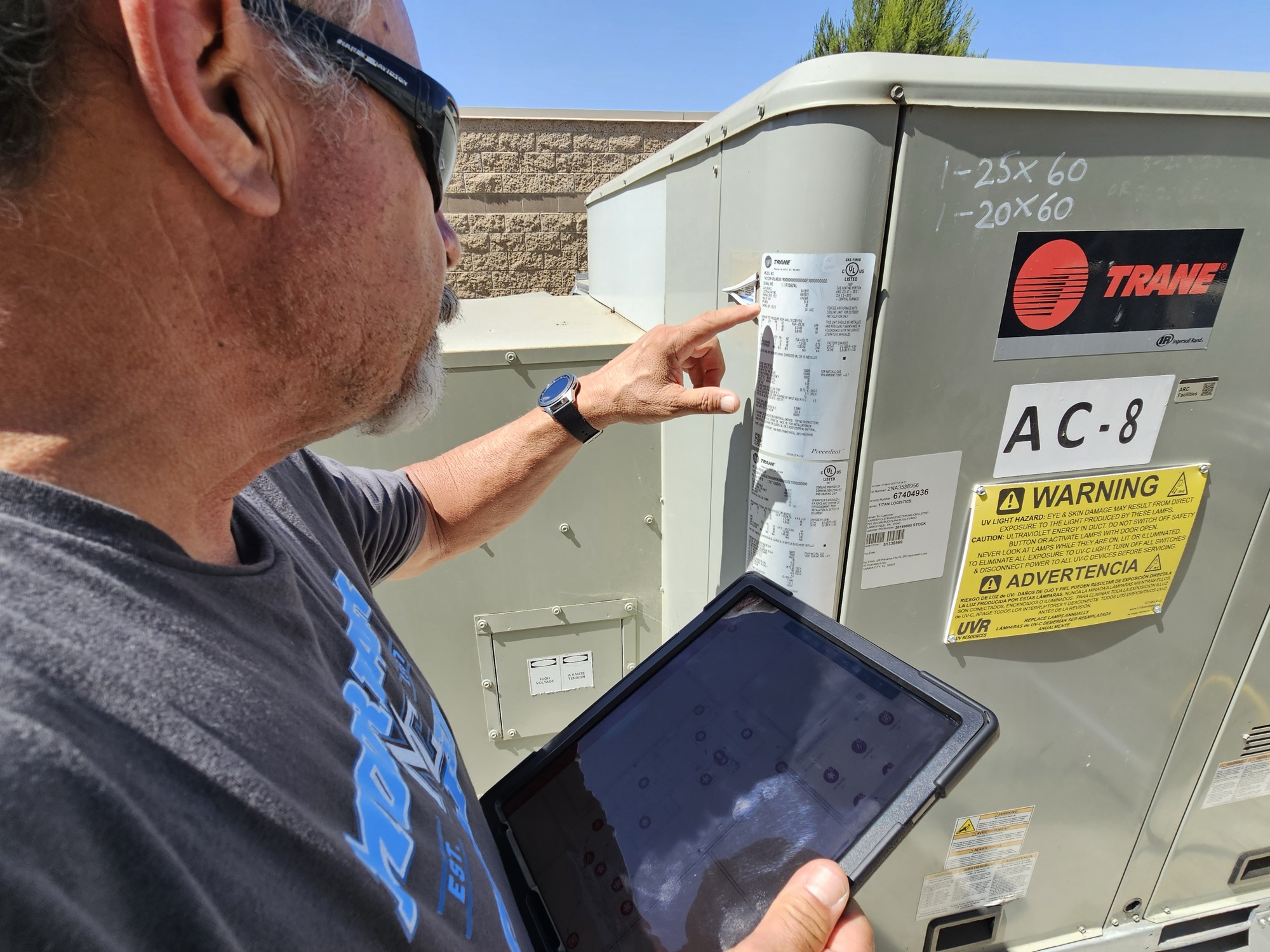
AI for technicians needs to focus on practical, intuitive applications that can improve workflow efficiency and reduce downtime without requiring significant training or time investment. Image: ARC Facilities
Organizations and individuals that commit the time and resources to lean into this technology can benefit greatly. Where many will see the greatest impact will be in what might be considered stealth AI. Software developers are using these new generative AI capabilities to subtly improve the tools we already use.
While AI isn’t likely to perform physical maintenance tasks any time soon — like fixing a rooftop air handler or replacing the fluids on a generator — there are several ways it can empower technicians:
- Instant access to knowledge: Imagine walking up to a piece of equipment and, without needing to input any queries, instantly having the system provide troubleshooting tips, parts schematics, or installation and warranty information. This capability is a major value-add AI can bring to FM, allowing technicians to access what they need without extensive searches.
- Predictive suggestions: Like personal devices that suggest frequently visited places when you get in the car, AI can anticipate technicians’ needs. Suppose a technician often checks certain metrics or performs specific tasks for a particular piece of equipment. AI can recognize this pattern and prompt those tasks, reducing the mental load and time spent finding information.
- Simplified mobile solutions: Today, most technicians carry smartphones. The challenge has been that many FM tools are too complex or weren’t designed with mobile use in mind, making them cumbersome for technicians to use them on the job. AI can streamline mobile apps to intuitively prompt the information needed, making it easy for technicians to complete tasks without being hindered by technology.
Shifting focus: AI tools that do the heavy lifting
For technicians, the goal isn’t to learn complex AI algorithms or to understand AI at a granular level. Instead, FM professionals benefit most from tools that “do the thinking” for them. AI can be integrated seamlessly, removing the need for technicians to learn coding, complex prompting, or system integration. It should simply work as an “assistant,” helping technicians find solutions on the fly without requiring deep interaction or customization.
Like Amazon’s intuitive product reminders: the system knows when certain supplies or parts may be needed and can proactively suggest restocking. This approach, which leverages AI to anticipate needs, can empower technicians to stay ahead without added complexity.
Mobile-first, technician-centric solutions

When entering an equipment status update, a mobile AI tool could prompt the technician with the most relevant fields or possible actions, such as suggesting preventive maintenance tasks based on recent activity. Image: ARC Facilities
While tablets are becoming more common, phones are still the go-to tool for most technicians. Many FM tools are still based on legacy designs with desktop use in mind and are not optimized for mobile. This lack of mobile functionality has been a barrier to FM AI adoption. To truly empower technicians, the industry must prioritize mobile-friendly, AI-enhanced solutions that are efficient and easy to use.
AI-powered mobile tools tailored to technicians could streamline workflows by making essential information accessible anytime, anywhere. When entering an equipment status update, a mobile AI tool could prompt the technician with the most relevant fields or possible actions, such as suggesting preventive maintenance tasks based on recent activity. This user-focused AI delivers technicians the information they need without unnecessary steps.
Balancing industry trends and technician realities
While it’s tempting to think of AI as a panacea for FM challenges, it’s essential to differentiate between high-level tech integrations suited for large-scale companies and the actionable tools that frontline technicians need. AI’s effectiveness in FM will depend not on just the needs of accounting teams or executives, but also on how well it optimizes workflows, reduces the burden of manual data entry, and supports technicians with accessible, mobile-first tools that bring intelligence directly to the field.
While organizations are busy implementing large scale AI tools for analysis and to improve decision-making, it is important to also remember empowering technicians with thoughtful, focused AI applications that save time, reduce errors, and improve safety by delivering critical information at the right moment.
About the Author
Jonathan Styrlund is a vice president at ARC Facilities. Styrlund joined ARC in 2001 and has managed the development of several of the company’s technology products. Today, he oversees development of the award-winning ARC Facilities solution, which uses AI and machine learning to allow facilities professionals to instantly access critical building information from any mobile device.