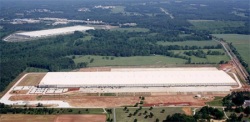
by Shane Henson — September 12, 2012—General Mills, an international producer and distributor of cereals, snacks and processed foods, recently announced that its new customer service facility in Fort Wayne, Indiana, has been awarded LEED Gold certification by the U.S. Green Building Council (USGBC). As an internationally recognized mark of excellence, the Leadership in Energy and Environmental Design (LEED) program provides building owners and operators with a framework for identifying and implementing practical and measurable green building design, construction, operations and maintenance solutions.
The newly opened facility is the largest warehouse and distribution center project in North America to achieve LEED Gold certification and the third largest in the world, says General Mills. The company’s customer service facility in Social Circle, Georgia, which opened in 2010, is reportedly the second largest in the United States and the fourth largest in the world.
According to General Mills, the building achieved LEED Gold, the second-to-highest rating awarded by the USGBC, by employing several efficiency technologies and environmentally friendly design elements, including:
- A white roof and 100% concrete paving that reflects sunlight to reduce radiant heat and air conditioning costs;
- Low-flow plumbing fixtures that reduce water use by 33%;
- Retention ponds that hold stormwater from the roof and paved areas for landscaping irrigation;
- Superior ventilation that exceeds fresh air requirements by 30%; and
- Energy-efficient light fixtures, occupancy sensors, high efficiency HVAC systems, roof-mounted up-blast exhaust fans and wall louvers, all of which make the facility 45% more energy efficient than the baseline model for industrial buildings.
- Low-flow plumbing fixtures that reduce water use by 33%;
Further, the project obtained LEED Gold certification for its environmentally conscious construction and operations, says General Mills.
- Eighty-five percent of the construction waste, totaling more than 596 tons of material, was diverted from landfills by sorting the materials and sending them to the appropriate recycling centers for reuse on other products.
- Forty-four percent of the construction materials were extracted, processed or manufactured within 500 miles of the project site.
- Green power certificates have been purchased for 70% of the building’s electrical usage, signifying an investment in future technologies of non-fossil fuel energy sources.
- Forty-four percent of the construction materials were extracted, processed or manufactured within 500 miles of the project site.
The facility also will use a centralized computer-based transportation system, which allows General Mills to map out the multiple destination points of the products being delivered, and to load more onto each truck. The result should be more efficient truck loads, more efficient shipments, and fewer trucks on the road.