by Stephen Meador — For most of human history, natural ventilation was the only way to dilute and flush air contaminants like odors, smoke, and other combustion by-products from an inhabited space. It was also a primary means of achieving thermal comfort through passive cooling, especially in climate regions that didn’t experience big swings in daily temperatures. For regions with dramatic temperature variations, such as desert climates, early builders learned how to use radiant exchange from massive floors, walls, and ceilings to keep occupants cool and comfortable. As time passed and multi-story buildings became common, natural ventilation could usually meet thermal comfort needs through passive cooling, if designed correctly. One common design included a building with a central atrium and a cupola on the roof to help induce drafts. In most designs, features such as windows, doors, corridors, stairways, skylights, and roof vents would be used to capture, direct, and exhaust outside air through a building. When natural ventilation couldn’t keep up with thermal comfort requirements in the workplace, employees were often dismissed once temperature and humidity reached excessive levels.
With the implementation of air conditioning and envelope improvements in the 20th century, things changed dramatically as interior conditions became more controllable through use of HVAC machinery. Buildings became better sealed and were often designed without operable windows, meaning infiltration of outside air was lessened. However, even with the advent of minimum ventilation rates in the 1970s (typically determined using the Ventilation Rate Procedure found in ASHRAE Standard 62.1), indoor air quality could often be unhealthy. By the mid-1980’s, a phenomenon known as “Sick Building Syndrome” (SBS) came into prominence, characterized by symptoms that include headache, sore throat, and nausea.
Advantages of natural ventilation
While studies have shown that mitigation approaches such as increasing window views, daylighting, and indoor plants can help mitigate SBS, increasing natural ventilation is the most effective approach, reducing symptoms by 15-70%. According to a 2015 study by the World Green Building Council, staffing costs typically account for about 90% of a building’s total lifecycle costs. It may come as no surprise then that natural and hybrid (or mixed-mode, i.e. mechanical + natural) ventilation systems can pay for themselves in a very short time, primarily through employee productivity gains. There are many other advantages to natural ventilation, including HVAC energy savings in the range of 47-79% when replacing or supplementing mechanical ventilation with natural or mixed-mode strategies. HVAC maintenance costs can also be reduced since filter changes and duct cleaning will be reduced or eliminated. According to a 2004 Carnegie Melon study, the average return on investment for natural ventilation or mixed-mode conditioning is 120% for retrofits and more than 400% for new construction.
Natural ventilation is made possible by differences in pressure, temperature, and humidity. Pressure differences arise when wind impacts the side of a building, creating higher pressure on the windward side and lower pressure on the leeward side. Depending on wind speed and direction, the air is driven through façade openings resulting in cross ventilation. Orientation can play a big role in cross ventilation, with the windward face of a naturally-ventilated building usually designed to be perpendicular to the summer wind. Differences in temperature and humidity can also drive natural ventilation. Interior air that is warmed and humidified by people, lighting, kitchen equipment, etc. becomes lighter than outside air and rises, exiting through skylights, roof vents, or other openings at various levels, while drawing in cooler air to replace it through openings below. This is called stack effect or chimney effect ventilation. One major difference between stack effect and cross ventilation is that stack effect ventilation can occur on hot summer days with no wind.
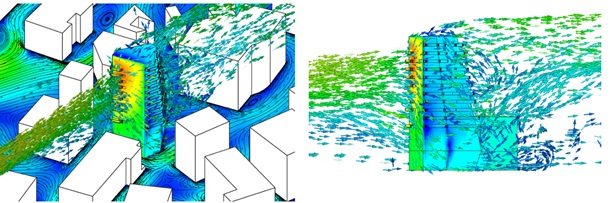
Figure 1. Computer simulation showing higher pressures caused by higher wind speeds, necessitating smaller window openings near the top.
Natural ventilation is not commonly utilized in commercial buildings in the United States. That’s due primarily to a lack of standardized guidance from building codes, regulators, and standards organizations about how best to incorporate natural or mixed-mode strategies into new building designs or retrofits. Still another big problem is the lack of user-friendly modeling tools. However, if natural ventilation experts can be engaged to conduct building modeling and analysis, they can often develop a robust ventilation strategy using a whole-building approach. For example, a tall building might experience higher wind speeds and greater pressure differences at the top of the building versus the bottom, meaning upper windows would need to be opened less and/or designed smaller than lower windows (see Figure 1). . These windows might be manually controlled using a red/green stoplight system for occupants or automatically controlled using a building automation system. With a mixed-mode ventilation system utilizing automatic controls, designers might include an interlock that prevents mechanical cooling from functioning while windows are open.
How to tell whether natural ventilation is right for your building
Whether a natural ventilation strategy is right for your building depends on a number of factors, including climate, building use, local surroundings, and building design and construction.
Temperature and humidity
First, temperature and humidity are important drivers. The higher the outdoor temperature and relative humidity levels, the lower the potential for a successful natural ventilation strategy. That said, natural ventilation strategies are very common in some South and Latin American countries in equatorial climates. Humidity is usually the key driver since it has such a large impact on thermal comfort and can’t be controlled using a pure natural ventilation strategy. If your building is located in an area with high summer humidity, you are better off exploring a mixed-mode ventilation strategy versus a straight natural ventilation strategy.
Building design and building use
Building design and use are also important drivers. Buildings that have operable windows, typically older or historic buildings, often make better candidates for cost-effective natural ventilation retrofits. Building shape or footprint is important because buildings can’t be excessively deep (usually 45 feet or less) because natural ventilation won’t reach the occupants in the building’s interior. Large rooms and buildings like shopping malls, meeting halls, sports arenas, museums, atriums, and common areas make excellent candidates for natural ventilation. Historic or protected buildings are also excellent candidates because walls and ceilings don’t need to be disturbed for machinery or ductwork, and retrofits can be completed quickly with minimal disruption for occupants since they aren’t typically forced to relocate (see Figure 2). Smaller spaces such as classrooms and offices can also perform well if the ventilation strategy is properly engineered. Buildings with stringent ventilation and thermal control requirements like restaurant kitchens, data centers, and most hospital spaces do not make the best candidates.
Building surroundings
Local surroundings are important, as well. Consideration must be given for noise and air pollution, as well as nearby landscape features. Air blockage from adjacent buildings and trees must be well-understood when developing a natural ventilation strategy. Still another consideration is the amount of man-made materials such as concrete, brick, asphalt, steel, and glass in your surroundings. Areas with an excess of these materials are vulnerable to the Urban Heat Island effect during the warm seasons, where urban area temperatures are substantially elevated compared to their suburban and rural surroundings. This can make thermal control within a naturally ventilated building even more challenging, although the building will arguably be more resilient in the event of an extended power loss. Heat Islands can also generate high ozone levels, increasing health risks to building occupants. Buildings located in densely populated urban areas often experience transit, construction, and landscape maintenance noise, as well as air pollution such as exhaust fumes, particulates, and odors. All of these factors can preclude or at least complicate natural ventilation strategies. For example, windows may need to be closed during air pollution alerts, peak commuting hours, or extreme temperatures.
Coming up with the right design for natural ventilation
Once you’ve determined that a natural or mixed-mode strategy might work for you, it’s best to engage professional designers who can model your building and provide a range of alternatives. However, if you have a candidate building and want to experiment with opening windows and making adjustments to systems and spaces, there are some building features and management approaches that can help ensure success.
First, opening multiple windows at varied elevations works best, with cooler supply air entering at lower levels and warmer exhaust air exiting at higher levels. Roof features such as vented skylights, ridge vents, and clerestory windows can also provide outlets for exhaust air. External shading features are helpful for minimizing solar heat gain while still allowing some level of daylighting, but they shouldn’t block air movement. Similarly, heat gain from interior lighting and plug loads should be minimized. The use of ceiling fans or whole-building fans will aid greatly in maintaining thermal comfort. In fact, air movement can extend the range of temperatures considered acceptable by occupants, especially if they are given some level of control, a phenomenon known as adaptive comfort. Fans can provide an effective temperature drop of up to 9°F while using roughly 10 percent of the energy required to operate an air conditioning system.
Opening up floor plans can improve pathways for airflow, as can opening doors, louvers, and transom windows. However, most fire codes won’t allow the use of adjustable transom windows because they can allow fire and smoke to travel between rooms. One primary purpose of fire codes is to prevent the migration of smoke and fire between interior spaces and floors, so natural ventilation strategies must always take fire codes into account. As an example, modern fire codes require doors to stairwells to remain closed, negating one historic approach to naturally ventilating buildings when stairways were used as exhaust paths. Some companies specializing in natural ventilation building products offer dual-purpose roof features that provide natural ventilation on a day-to-day basis but can also be controlled during a fire to provide smoke-free escape routes for building occupants. This can help mitigate the most common threat to survival in a fire, namely smoke and toxic fumes versus heat and flames.
If you are ultimately left wondering if your building occupants will have to accept a certain level of discomfort to enjoy the benefits of natural ventilation, industry experts say no. While temperatures may fluctuate more than they do with mechanical ventilation systems, overall comfort can be higher if the control strategy is well-designed. Additionally, natural ventilation can provide a higher degree of user-system interaction and individual control of the indoor climate, which usually leads to happier occupants.
About the author
Stephen Meador, CEM®, LEED AP O+M is a Facility Management Consultant at Facility Engineering Associates where he helps clients improve the way they manage their facilities. Stephen has degrees in Mechanical and Environmental Health Engineering and works under the facility consulting services line that specializes in facility asset management, building energy management, and sustainability services.
Facility Engineering Associates wishes to thank Windowmaster International for providing content support for this article.